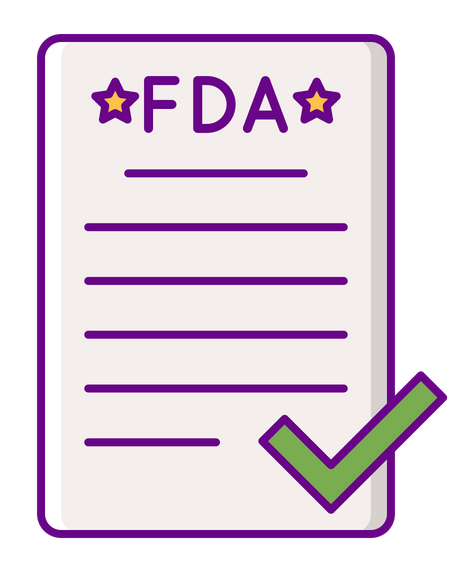
FDA
TOTAL COMPLIANCE FDA program
A new ExportUSA service to make preparation of a food safety plan and drafting of a HARPC manual easier, faster and cheaper
https://www.exportusa.eu/food-safety-plan-preparation-FSMA-FSVP.phpThe FDA - Food and Drug Administration is the body that regulates the distribution of food products in the US.
Normally the regulatory approach of the FDA, like that of other American government agencies, is to issue standards, let the manufacturer adjust their products to them, and then check compliance therewith.
However, in the case of canned or vacuum-packed food products, the FDA adopts a different approach, which we could define as prior authorization. The risk is that botulism can occur in the presence of a production process that does not guarantee a good sterilization.
Autoclaves are the fulcrum of the food product sterilization process, and the Food and Drug Administration requires the validation of the autoclaves used in the production of risky food products, such as those canned or vacuum-packed.
ExportUSA has selected technical partners with a long experience in the autoclave validation process to guarantee the sterilization of the food products that are to be imported into the United States. The specialized staff of ExportUSA combines a consolidated experience in the technical analysis of the production process of food products with the knowledge of the approval procedures by the FDA.
We offer you the guarantee that you can import your food products into the United States without the risk of your shipment being seized at Customs and your company being blacklisted by the FDA.
Levels of Guaranteed Sterility
The level of microbial inactivation can be described by an exponential function of guarantee of sterility or SAL, Sterility Assurance Level. A SAL of 10-6 means that the probability of finding a single live microorganism in a sterilized item is one in a million after the item has undergone a sterilization process. A SAL of 10-3 means that the probability of finding a single live organism present after sterilization is 1 in 1000.
Thermal resistance characteristics
The thermal resistance of specific microorganisms is characterized by two typical parameters, namely the ìD-valueî and the ìZ-valueî. D-value is the time in minutes, at a specific temperature, to reduce the surviving microbial population by 1-log. Z-value is the temperature change required to cause a 1-log reduction in D-value.
Operational Qualification (OQ)
The OQ process is intended to demonstrate that the autoclave components are functioning properly and that the autoclave is deemed ready for use or for a load test.
Empty Chamber Distribution tests
The main goal is to show that the chamber offers a uniform sterilization environment. Performance Qualification (PQ) - Steam penetration test Steam penetration tests are then conducted on each load. This is a time-consuming process, especially if you have a significant number of items to sterilize. It is necessary to determine which load elements are the most difficult to sterilize and whose position inside the elements presents the most critical conditions in terms of sterilization.
Load the configurations
Another critical variable is related to the load configurations of the autoclaves, which can be fixed or flexible. A fixed load configuration means that the load to be sterilized will be identical for all future sterilization steps, and that the load is placed in the autoclave chamber identically for all future processing steps.
Lately, the FDA has begun requesting an additional study with respect to the TEMPERATURE DISTRIBUTION STUDY and the HEAT PENETRATION STUDY. The HEAT DISTRIBUTION STUDY is normally required when there are air/steam-type autoclaves. It is a much more complex and articulated study than the first two.
A new ExportUSA service to make preparation of a food safety plan and drafting of a HARPC manual easier, faster and cheaper
https://www.exportusa.eu/food-safety-plan-preparation-FSMA-FSVP.php